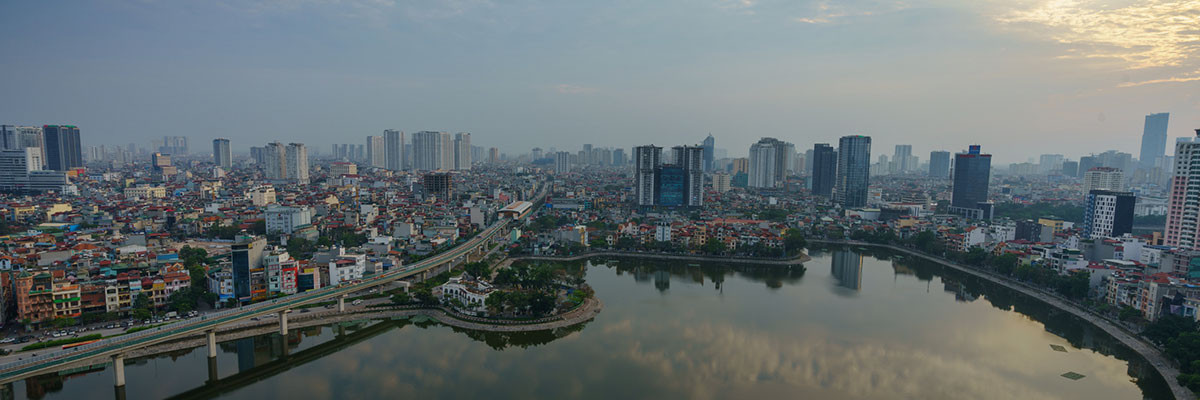
Authors
-
Jeremy Prepscius
Former Vice President, Asia-Pacific, BSR
2019 continued the existing movement of supply chains out of China. This movement was driven in part by rising wage rates in China, a Chinese focus on reducing pollution, and the government policy to export low value-added manufacturing processes, and it was further exacerbated by trade tensions. As the exodus of manufacturing continued and accelerated, both manufacturing groups and global buyers sought opportunities to re-globalize their value chains. This Globalization 2.0 trend will continue over the coming decade.
Now, 2020 brings us COVID-19. The impacts of consolidated risks in global supply chains are thrown into even sharper relief. Consequently, risk mitigation and the need to build resilience into global supply chains are going to accelerate the re-globalization of these supply chains.
This means markets which already are sourcing platforms (e.g., Vietnam) are going to be seeing considerable growth, while more nascent markets, from Myanmar to Uzbekistan, will be increasingly on the map. It also means suppliers and buyers will be encountering new challenges in new markets as they set up shop.
Here are six sustainability considerations to help your company create Globalization 2.0 plans which can help achieve long-term success.
-
Understand your own intent. It may seem obvious, but it’s still worth stating: your starting point should be understanding the business intent behind a supply-base diversification strategy. Pricing, delivery, quality, mechanization, de-carbonization, proximity and access to markets, resilience in key component manufacturing, risk diversification, and alignment with strategic partners may be all part of the business purpose and should provide context for the subsequent due diligence.
-
Look broadly at the sustainability and human rights risks of a country. The tools you used to qualify a factory in the early 2000s are not enough anymore. A factory audit isn’t sufficient and you should be aware of the broader environmental, social, and governance risks of the country in which you/your supply chain will be operating. Understand and map the relevant country risks—from pollution, natural disasters, and labor and employment standards to graft and corruption. These are just a few risk areas—these will vary by country and certainly should be integrated into risk frameworks and due diligence processes. Understanding (and engaging) key stakeholders with relevant knowledge can help you understand these risk areas. Surprises are not excusable.
-
Understand your (potential) partner(s). Ask the right questions in order to understand exactly who you are doing business with and to determine your risk exposure. Who are the beneficial owners of the partner? What is the land/industrial zone permitting and history? What are the current relationships and reputation of that partner, based on past history (if any) in the sourcing country? Does this supply chain partner share your values and will they be a trusted partner in navigating the (inevitably) changing environment and the next crisis?
-
Do your supplier due diligence. Ensure a high-quality assessment of actual working conditions, management attitudes, and factory systems. Auditable information (fact gathering) on all the traditional compliance issues is important and a solid assessment of environmental (e.g., waste, energy, etc.), social (e.g., employee welfare, health and safety, human rights) and governance issues (e.g., grievance systems, anti-corruption, community engagement and transparency) is important. So too is the social dialogue inside the factory (industrial dialogue, communication systems, harassment issues) and the investment of the supplier in human capital (from hiring to training). Robustness of management systems and the qualifications of the actual leaders underlie the resilience of your partner(s).
-
Plan (and budget) for developing supplier resilience. How well is the supplier positioned to work through the key risk factors inherent in the country? Is the supplier making the investments which will enable resilience through critical times? Investments in grievance and dispute resolution systems, worker engagement, supervisor skills, and internal dialogue help mitigate risks during times of labor strife. Internal controls and strong external community relations enable resilience during times of changing external governance. Preparation and planning integrated into disaster risk reduction plans are important for preparing for weather, health, or other possible risk scenarios.
-
Plan (and budget) for buyer impact. What scenarios are you planning for: disasters, carbon prices, labor shortages, industrial action, rapid market expansion? How well-prepared will you, as the buyer, be in terms of expectations for local transparency and community needs? What opportunities are there for collaborative industry approaches or public-private partnerships? How might these create value for you or your supply chain? Plan for your own opportunities and needs in terms of people, resources, transparency, and stakeholder engagement.
In short, think beyond compliance, understand the “total cost of ownership” of your supply chain plans, and know that your partners are aligned with your vision, values, and goals. Build resilience and plan for the next disruption. As Globalization 2.0 continues and supply chains diversify in new locations, let’s learn from the experience of the past three decades. Companies should continue to try to holistically understand and mitigate risk while finding collaborative opportunities for impact. At BSR, we know these actions work and can help build more equitable and resilient supply chains.
Topics
Let’s talk about how BSR can help you to transform your business and achieve your sustainability goals.