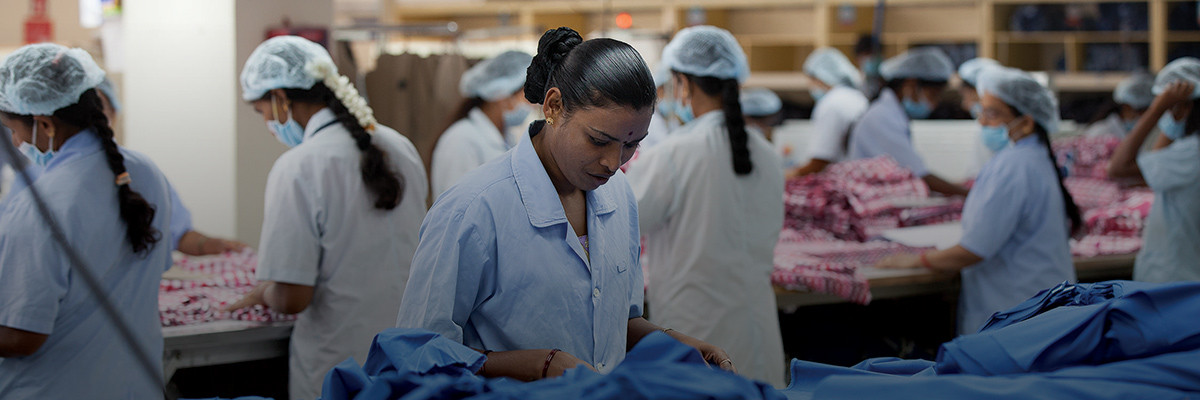
Authors
-
Marat Yu
Former Manager, BSR
In October 2015, the Evidence Project/RAISE Health, in partnership with HERproject, released the Workplace Health Facility Guidelines and Management Benchmarks to help workplaces improve their onsite health services. With the support of Takeda Pharmaceutical Company and UK aid, BSR piloted the benchmarks with Change Associates in 15 ready-made garment factories in Bangladesh from September to November 2015.
To help companies use the guidelines, HERproject and the Evidence Project have produced a scorecard that allows managers to assess the three key areas pertinent to workers’ health: clinical good practices, management systems, and corporate leadership. The scorecard enables managers to identify where they stand and determine what next steps are feasible to improve workplace health.
Based on the pilot learnings and the scorecard, we have five suggestions for companies to enhance workers’ health in their supply chains:
- Work on the basics: The basic quality of a clinic sends an important signal to workers that management cares about their health. A few of the clinics we observed were not kept clean, were stocked with expired medicines, and lacked ambient lighting and private space for client examinations. Getting the fundamentals rights is easy and requires minimal resources.
- Then, go beyond occupational health: Companies should consider how their policies and services can promote preventive healthcare for workers. Many of the pilot factories were content to meet only minimum compliance standards, which focus predominantly on occupational health, and sidelined other primary health services. For instance, only 2 out of 15 clinics provided sanitary napkins. Given that the majority of workers are women, companies could play a key role to enable access to reproductive health products and services.
- Secure management’s buy-in: In 3 out of 15 factories, a self assessment was introduced prior to the external assessment. The self assessment provided an opportunity for management and clinic staff to reflect on the quality and capacity of health services provided onsite, and we found that after doing the self assessment, factories were more motivated to drive their own improvement processes.
- Invest in health providers: With a few exceptions, health providers, usually nurses and paramedics, were not given clear responsibility and failed to proactively anticipate and address health needs. Performance was particularly weak in clinic management and health promotion. By investing in professional training and on-the-job coaching, companies can turn these personnel into valuable business resources. Experience around the world suggests that better trained nurses can not only improve the health of workers, but also help improve occupational health compliance.
- Use external service providers: In the case where factories feel constrained to provide certain services, they can connect with external service providers in the community. For example, one factory collaborated with the Smiling Sun clinic (a US aid- and DFID-supported initiative) to provide family planning products and counseling to workers in need.
Too often, management does not recognize the need and benefits of proactively managing its health staff and activities, but with the right management support, onsite health providers can contribute to the overall productivity of a workplace—and healthier, happier workers.
Let’s talk about how BSR can help you to transform your business and achieve your sustainability goals.